Introduction
Yttrium aluminum garnet (YAG) is a widely used laser material known for its excellent optical properties and thermal stability. It is commonly used in solid-state lasers, such as Nd:YAG lasers, and has applications in various fields, including medical, industrial, and scientific research. This article aims to provide a comprehensive explanation of the manufacturing process of yttrium aluminum garnet.
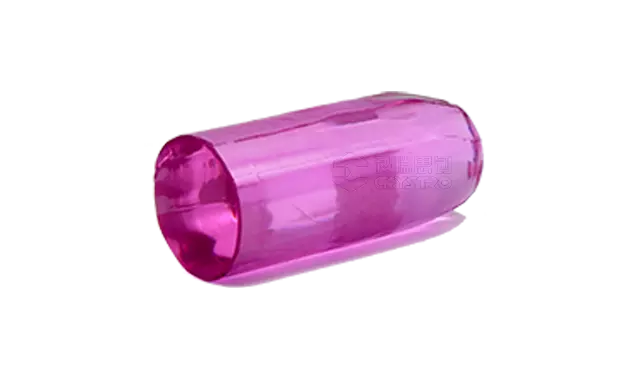
Synthesis of Yttrium Aluminum Garnet (YAG)
Raw Materials: The synthesis of yttrium aluminum garnet typically starts with high-purity raw materials, including yttrium oxide (Y2O3) and aluminum oxide (Al2O3). These materials are mixed together in precise stoichiometric ratios to ensure the desired composition of YAG.
Weighing and Mixing: The raw materials are accurately weighed based on the desired composition and mixed together thoroughly. This step is critical to achieve uniform distribution of the elements within the final YAG crystal.
Heating and Fusion: The mixed powders are then placed in a crucible made of high-temperature resistant material, such as graphite or alumina. The crucible is heated in a controlled atmosphere, typically using a high-temperature furnace. The temperature is raised gradually to facilitate fusion and homogenization of the powders.
Single Crystal Growth: Yttrium aluminum garnet is typically grown as a single crystal using various techniques, including the Czochralski method and the Bridgman-Stockbarger method. In the Czochralski method, the crucible containing the molten YAG is slowly cooled while a seed crystal is slowly withdrawn from the melt, allowing a larger crystal to form. The Bridgman-Stockbarger method involves moving the crucible through a temperature gradient, causing the YAG melt to solidify into a single crystal.
Annealing: After the crystal growth process, the YAG crystal may undergo annealing. This involves subjecting the crystal to controlled heating and cooling cycles to relieve internal stresses and enhance its optical properties.
Cutting and Machining: Once the YAG crystal is grown and annealed, it is cut into the desired shape using diamond saws or laser cutting techniques. The cut YAG crystal may then undergo additional machining processes, such as grinding and polishing, to achieve the desired optical quality.
Quality Control and Characterization
Throughout the manufacturing process, various quality control measures are taken to ensure the final YAG crystal meets the required specifications. This includes rigorous testing and characterization of the chemical composition, crystal structure, optical properties, and thermal properties of the YAG material.
Conclusion
Yttrium aluminum garnet (YAG) is a valuable laser material used in numerous applications. The synthesis of YAG involves precise mixing of high-purity yttrium oxide and aluminum oxide, followed by heating, fusion, single crystal growth, and annealing. Quality control measures are implemented throughout the manufacturing process to ensure the final YAG crystal meets the desired specifications. By understanding the manufacturing process of YAG, we can appreciate the intricate steps involved in producing this important laser material.